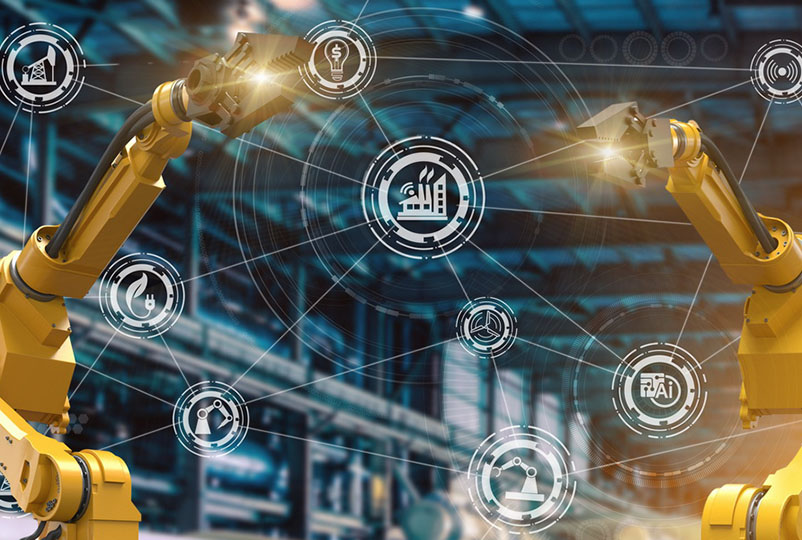
Industrial Automation
In the dynamic landscape of industrial automation, connectors serve as vital components that underpin seamless communication, signal transmission, and power distribution within complex systems. As the industrial automation market continues to evolve, connector requirements are shaped by the following development trends:
High-Speed Data Transmission: The rise of Industry 4.0 and the Industrial Internet of Things (IIoT) has ushered in an era of data-driven automation. Connectors must accommodate high-speed data transmission to facilitate real-time monitoring, control, and analysis of industrial processes.
Ethernet and Fieldbus Connectivity: Industrial Ethernet protocols, such as EtherCAT, PROFINET, and Ethernet/IP, are increasingly utilized for communication between automation devices. Connectors need to support these protocols while ensuring reliable and low-latency data exchange.
Miniaturization and High-Density: Industrial automation systems demand compact and high-density connectors to optimize space utilization on factory floors and control panels. Miniaturized connectors help accommodate the growing number of components in confined spaces.
Harsh Environment Durability: Industrial settings pose challenging conditions, including temperature extremes, vibrations, and exposure to chemicals. Connectors must be rugged and durable, capable of withstanding harsh environments and maintaining reliable connections.
Secure Connections: As automation systems become more interconnected, security becomes paramount. Connectors should incorporate secure locking mechanisms to prevent unauthorized access and maintain the integrity of the industrial network.
Modularity and Flexibility: Automation systems are designed for scalability and adaptability. Connectors with modular designs enable easy expansion and configuration changes, supporting the evolving needs of industrial processes.
IP67/IP68 Protection: In applications where connectors are exposed to water and dust, IP67 and IP68 rated connectors ensure reliable performance in challenging environments, reducing downtime and maintenance.
EMC/EMI Shielding: Industrial automation environments are susceptible to electromagnetic interference (EMI) and electromagnetic compatibility (EMC) challenges. Connectors with effective shielding mechanisms minimize the impact of EMI on sensitive equipment.
Hot Swapping and Redundancy: To minimize downtime, connectors should support hot swapping, allowing components to be replaced without shutting down the entire system. Redundant connectors also ensure continuity in case of a connector failure.
Modbus and IO-Link Integration: Legacy systems and newer technologies coexist in industrial automation. Connectors must accommodate various communication protocols, including Modbus and IO-Link, to facilitate seamless integration.
Industry-Specific Standards: Different industrial sectors, such as automotive, manufacturing, and energy, have unique requirements. Connectors must adhere to industry-specific standards to ensure compatibility and interoperability.
Predictive Maintenance: Industrial automation is moving towards predictive maintenance to optimize uptime. Connectors with diagnostic capabilities can provide insights into connector health, enabling maintenance before failure occurs.
In summary, the industrial automation market is driven by data-driven processes, connectivity demands, and the need for robust solutions. Connectors play a pivotal role by meeting requirements for high-speed data transmission, resilience in harsh environments, security, and compatibility with various communication protocols. As the industrial landscape continues to evolve, connectors will remain essential in driving efficiency, connectivity, and innovation in automation systems.
Related Products
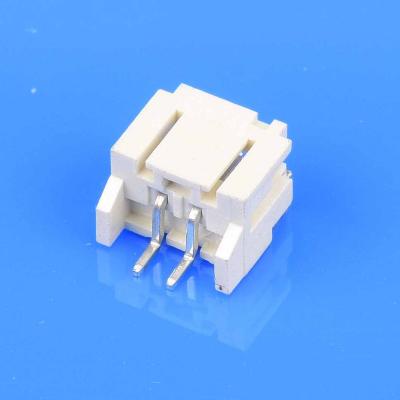
( 2 . 0mm )
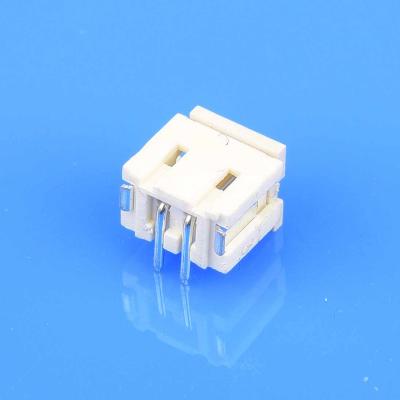
( 1 . 5mm )